Modern Manufacturing
Aquasgroup Zero Liquid Discharge Systems – Manufacturing – Metal Finishing
“Send it down the drain”
Sound familiar? Times are changing fast. This common practice and the lack of thought behind it is in trouble. In this article, I will explain why.
What is wastewater?
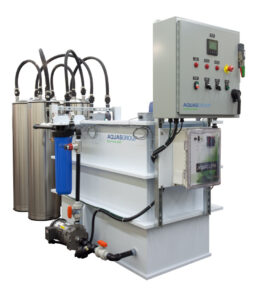
GFS Rinse Water Recycling System
In manufacturing, there are numerous applications that use water for rinsing manufactured parts following processes that contain chemicals, both organic and inorganic. Simply stated, organic processes include contaminants, typically oil, originating from carbon. Inorganic contaminants are from the mineral world, including cadmium, chrome, nickel and copper, to name just a few. Rinse water, once contaminated, becomes wastewater and needs to be managed under the Clean Water Act regulations.
Since the inception of the Clean Water Act, by EPA, back in the late ‘70’s, manufacturers have been required to maintain pretreatment discharge permits for any and all wastewater discharged from the facility. Initially, waste water was discharged either to a river, a septic system, or to the sewer, also known as the POTW. The POTW then discharges to a river typically, or to an ocean.
Over time, the established rules, and in this case, the discharge limits, have become increasingly stringent. Whereas they originally were stated in “parts per million”, or “ppm”, it is typical for them to have been decreased a full order of magnitude, whereby today it is not uncommon for limits in the “parts per billion”, or “ppb”, to be enforced. The point is, the required limits for discharge compliance are only becoming ever more stringent. The risks, and associated costs of non-compliance are increasing over time, at an ever-increasing rate.
In parallel to what might be fairly considered an overzealous regulatory body, we also have ESG, or Environmental Social Governance advocates and a powerful environmental awareness taking place throughout society. The abridged take away is that if you are a manufacturer, you’d best think twice about the necessity of sending waste water from manufacturing operations to drain without considering your options first. If you want to attract young employees, you will need to think as they do, that you will always do what is required to protect the environment first and that you will regard clean water as the increasingly finite resource that it is.
What is interesting is that unknowingly, we pay more for bottled water oftentimes than we do for gasoline! Based on a 16 ounce bottle of water at $.89 and gasoline at $4/gallon, we are paying over $7.00 for a gallon equivalent of bottled water!
Where do we go from here? We are fast approaching the day where an ever-increasing number of manufacturers are embracing rinse water recycling and by doing so, they are discovering its’ numerous additional benefits.
Where do we go from here? We are fast approaching the day where an ever-increasing number of manufacturers are embracing rinse water recycling and by doing so, they are discovering its’ numerous additional benefits.
How should we plan for the future?
Is it likely that the future of manufacturing will have no drains? Based upon the burgeoning environmental awareness alone, and the rate of its rise in popular thought, I believe that this is a given. The rate of implementation may vary region to region, but the writing is on the wall.
If you are building a new facility, or adding on to an existing one, consider the daily volume of process rinse water that will be required. If you need assistance, seek it out in order to form a water management plan. In general terms, if you will be generating less than 5000 GPD, save yourself the cost of a permitted discharge.
For more information on what is possible in your manufacturing operation, please contact us. We will be happy to make our recommendations.
Engineering
Nicholas Paolo, Jr.
President / Engineering
Mailing Address:
AQUASGROUP
830 Waterman Avenue
East Providence, RI 02914-1728