Parts Washing and Flushing Systems
Aqueous Industrial Parts Washing & Flushing Systems:
Aqueous industrial parts washing and flushing systems are essential in industries where cleanliness is critical to the performance, safety, and longevity of components. Sectors such as aerospace, medical device manufacturing, hydraulics, automotive, electronics, and precision machining demand strict cleanliness standards to ensure that parts operate at peak efficiency, free of contaminants like oils, metal shavings, FOD and other residues.
These water-based systems are designed to meet the unique requirements of these high-stakes industries, combining advanced cleaning technology with environmental responsibility. By leveraging water-based solutions enhanced with detergents, agitation, and filtration, aqueous cleaning systems deliver superior results while protecting delicate or sensitive materials from damage caused by harsh chemicals.
Precision Cleaning Across Industries
Different industries have distinct cleanliness needs, but all require highly reliable, consistent cleaning processes to ensure parts meet stringent quality standards. Aqueous cleaning systems can be tailored to address the specific challenges of each sector:
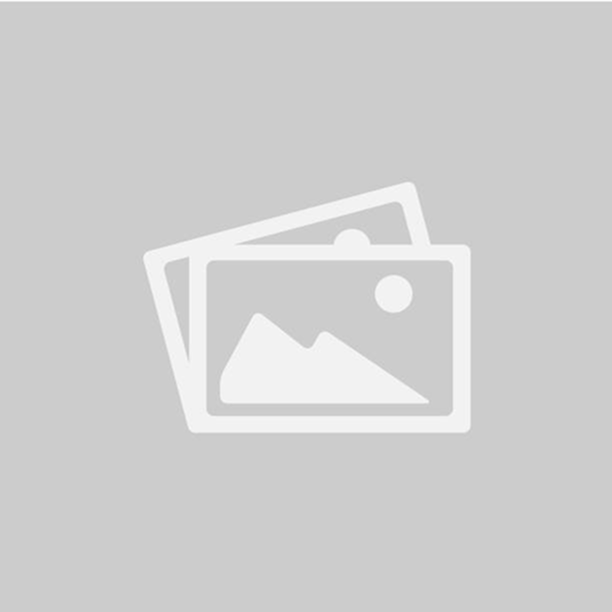
Aerospace
In the aerospace industry, even microscopic particles or residual contaminants can cause part failure or degrade performance. Aqueous cleaning systems remove oils, debris, and machining residues from critical components like turbine blades, hydraulic actuators, and landing gear to ensure safe and reliable operation.
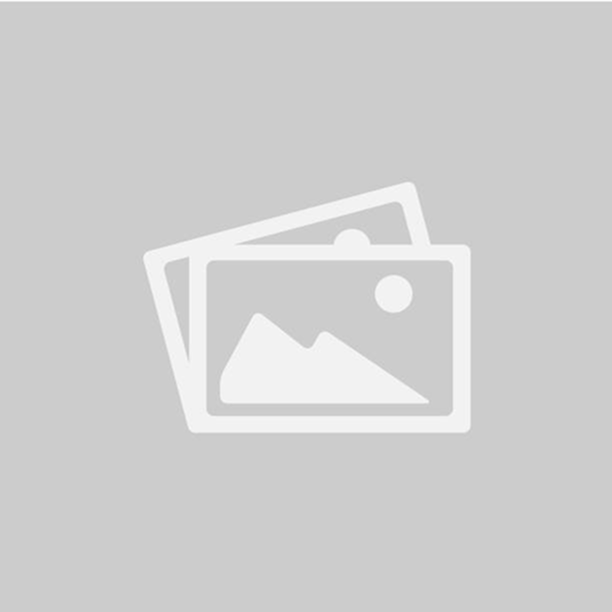
Medical Devices
For medical devices, cleanliness is paramount to avoid contamination that could affect patient safety. Aqueous systems are ideal for cleaning surgical instruments, implants, and precision components, ensuring sterility and compliance with regulatory standards.
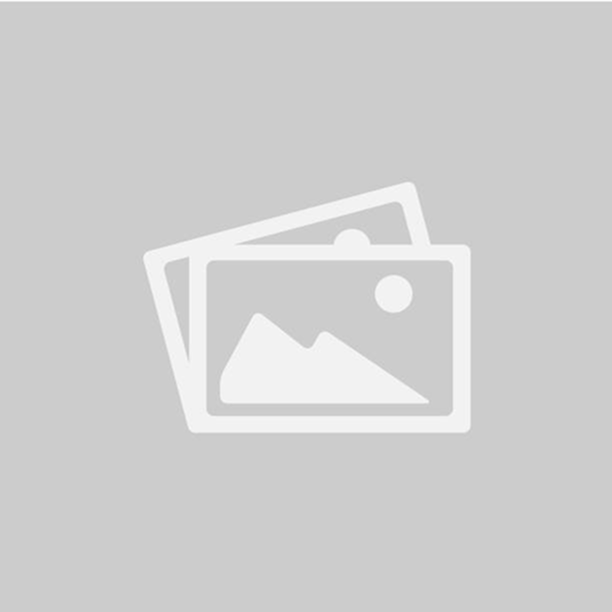
Hydraulics
Hydraulic systems rely on clean components to function without leaks, wear, or contamination. Aqueous cleaning systems remove metal shavings, oils, and particulate matter from hydraulic valves, pumps, and cylinders, ensuring proper sealing and performance.
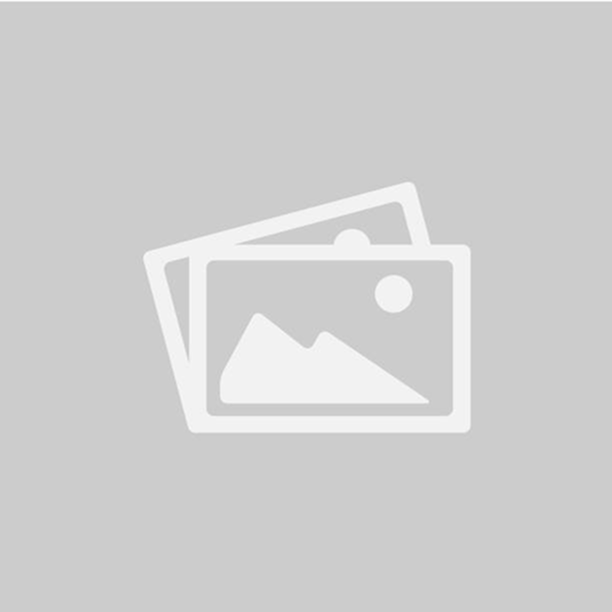
Automotive
In the automotive industry, precision cleaning is required for engine parts, fuel injectors, transmission components, and electronic systems. Aqueous cleaning systems are widely used to remove manufacturing residues that could impair function or durability.
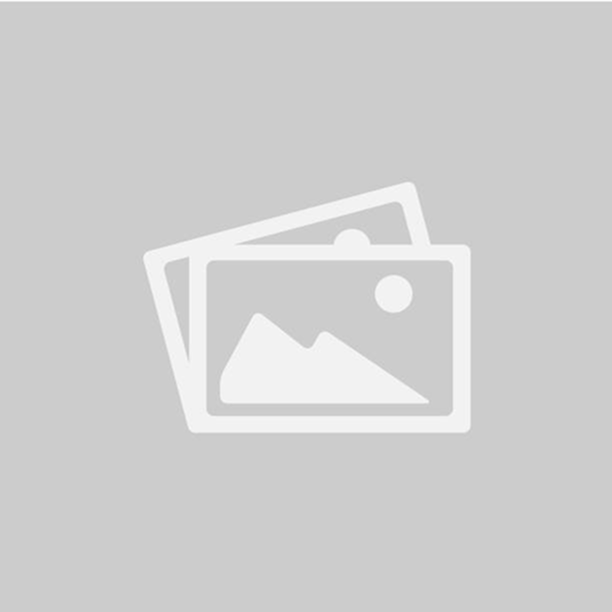
Electronics
For electronic components, even the smallest contaminants can cause malfunctions. Aqueous systems provide precise, gentle cleaning of circuit boards, sensors, and other delicate parts, preventing shorts, corrosion, or performance issues.
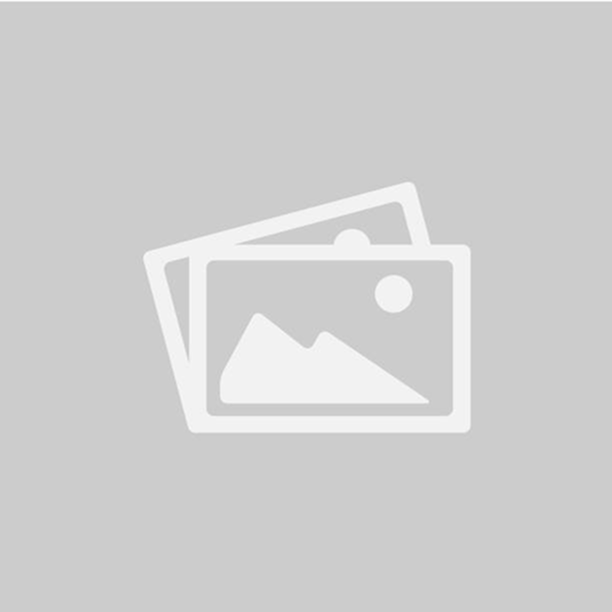
Precision Machining
Precision-machined parts, especially those used in high-performance applications, require meticulous cleaning to remove machining fluids, metal chips, and other contaminants. Aqueous cleaning systems provide thorough cleaning without damaging the fine tolerances and surfaces critical to these parts.
Different Levels of Cleaning: Tailored for Every Stage
Aqueous cleaning systems are engineered to meet varying levels of cleanliness required at different stages of production:
1. General Purpose Cleaning
General purpose cleaning is used to remove visible contaminants like oils, lubricants, and large debris. It is typically employed early in the manufacturing process to prepare parts for further machining, assembly, or finishing.
Applications
Pre-machining cleaning, routine maintenance, and removal of gross contamination in aerospace, automotive, and hydraulic systems.
Equipment
Spray or immersion-based systems, often in batch mode, using DI water or water-based detergents for efficient removal of contaminants.
2. Interstage Cleaning
Interstage cleaning is performed between production or assembly steps to ensure parts are free of contaminants before precision operations like welding, coating, or sealing.
Applications
In aerospace, interstage cleaning is crucial for turbine components before final assembly; in medical devices, it ensures sterility between processing steps.
Equipment
Advanced spray, immersion, or ultrasonic systems with multi-stage filtration and precise control over cleaning parameters.
3. Final Precision Cleaning
Final precision cleaning delivers the highest level of cleanliness, ensuring that even microscopic particles, oils, and residues are removed before final assembly or shipment.
Applications
Aerospace turbine blades, medical implants, automotive fuel injectors, and electronic circuit boards.
Equipment
Ultrasonic cleaners and multi-stage aqueous systems that incorporate deionized water for final rinsing to remove any remaining contaminants.
Batch Cleaning vs. Single-Piece Flow: Optimizing for Your Process
Industries with high production volumes, such as automotive and hydraulic systems, may opt for batch cleaning, which allows for multiple parts to be cleaned in a single cycle, maximizing throughput and reducing time.
Batch Cleaning Advantages
High-volume production, cost-effective for cleaning large numbers of parts, and ideal for industries where multiple components are processed simultaneously.
However, industries such as aerospace, medical devices, and precision machining often require single-piece flow cleaning to ensure that each part receives individualized attention, ensuring precise cleaning for high-value or sensitive components.
Single-Piece Flow Advantages
Greater control over the cleaning process for each part, ideal for industries where precision and quality are paramount, such as in aerospace and medical devices.
Importance of Process Consistency and Equipment Design
Maintaining process consistency is critical across all industries to ensure reliable, repeatable cleaning results. Inconsistent cleaning can lead to product failure, safety risks, or compromised performance, particularly in sectors like aerospace and medical devices.
Advanced Equipment Design
Aqueous cleaning systems must deliver uniform results. Features such as programmable wash cycles, precision-controlled spray nozzles, and automated handling ensure each part—whether in a batch or single-piece flow—receives the correct cleaning treatment.
Filtration and Water Quality
Appropriately designed filtration systems ensure contaminants are removed from wash and rinse cycles, preventing recontamination of parts and preserving wash solution and rinse water quality throughout the process.
Temperature and Pressure Control
Precise control over water temperature and pressure is essential for cleaning complex geometries and sensitive materials, ensuring contaminants are thoroughly removed without damaging the parts.
Automation and Monitoring
Real-time monitoring of cleaning parameters, such as detergent concentration and cycle time, ensures that every part is cleaned to the exact specifications required for the application.
The Role of Water in Aqueous Cleaning Systems
Water is the primary cleaning agent in aqueous systems, offering an environmentally friendly, non-toxic alternative to solvent-based cleaning methods. Water’s versatility allows for the removal of a wide range of contaminants, making it ideal for cleaning components across diverse industries. Used on its own or combined with detergents, filtration, and agitation (such as ultrasonic cleaning), water provides an effective means of dislodging and removing contaminants from even the most intricate parts.
Benefits of Closed-Loop Water Recycling Systems
Closed-loop water recycling systems enhance both the efficiency and sustainability of aqueous cleaning processes by capturing, filtering, and reusing water:
Water Conservation
Recycling water reduces the demand for fresh water, a critical consideration in high-volume industries like automotive and aerospace.
Cost Savings
Closed-loop systems significantly reduce the costs associated with fresh water use and wastewater disposal.
Environmental Impact
By minimizing water waste and reducing environmental contamination, closed-loop systems help industries meet sustainability and regulatory requirements.
Consistent Water Quality
Advanced filtration systems in closed-loop systems maintain high water quality throughout the cleaning process, ensuring consistent, reliable cleaning results.
Economical Recycling
Proper system design is essential for the economical recycling of water. Closed-loop systems are engineered to optimize filtration, reduce energy consumption, and lower operational costs, making them a cost-effective solution for industries where water usage is high.
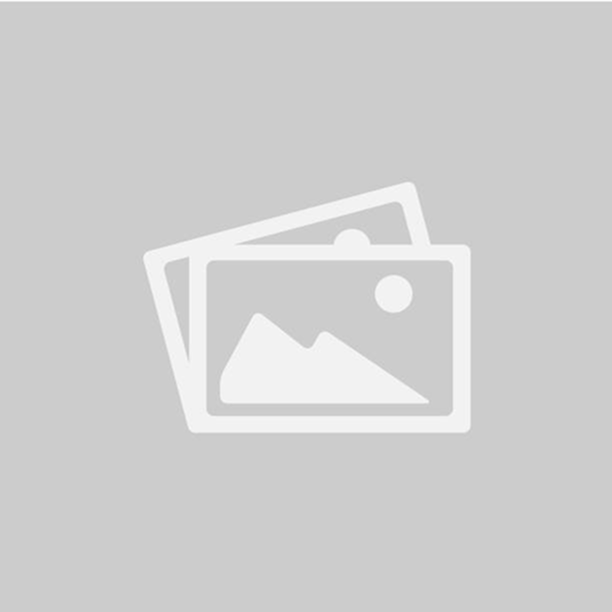
Conclusion
Aqueous industrial parts washing and flushing systems are essential for industries that demand the highest cleanliness standards, including aerospace, medical devices, hydraulics, automotive, electronics, and precision machining. By offering tailored cleaning solutions for general, interstage, and final precision cleaning, these systems ensure components are free of contaminants at every stage of production. The choice between batch cleaning and single-piece flow allows for flexibility depending on the industry’s volume and precision requirements. Combined with advanced equipment design and closed-loop water recycling systems, aqueous cleaning provides an environmentally responsible and cost-effective solution to meet today’s demanding industrial standards.