Electropolishing Process: Precision Finishing for High-Performance Applications
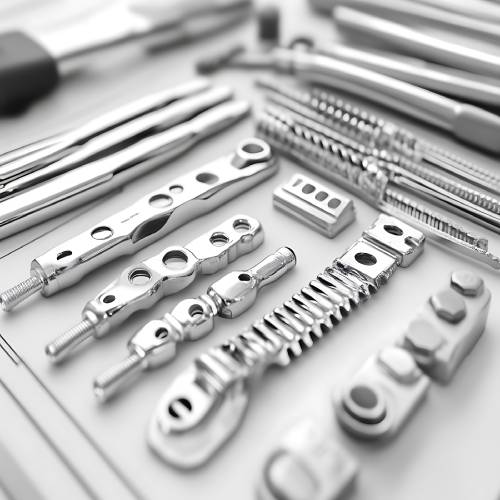
Mailing Address:
Corporate Headquarters & Fabrication Division
41 Commercial Way
East Providence, RI 02914
Water Technologies & Service Division
830 Waterman Avenue
East Providence, RI 02914