Vibratory Deburring Recycling
Clogged drains, high chemical costs and regulatory compliance are realities that challenge manufacturers when discharging waste water from vibratory deburring processes.
Vibratory deburring involves the use of abrasive media, a detergent, aka compound, and water to affect the surface of manufactured parts. Performed in vibratory tubs or bowls, there are various forms of how Vibratory Deburring Systems are designed centered around the amount of energy applied (low energy versus high energy) to affect process time.
Water is continuously contaminated in the deburring process as a result of the break down of abrasive media and the products being processed.
Over the past 70 years, waste water from Vibratory Deburring aplications has been primarily pretreated and then discharged to the sewer. The problems associated with this include clogged drains, escalating costs of compound and the increasing cost of regulatory compliance.
Cost effective recycling of Vibratory Deburring is now taking hold throughout major manufacturers’ facilities. The numerous benefits include:
- Elimination of drains and regulated discharges
- Enhanced process control and quality
- Lowered operating costs realized through compound, water and compliance costs
- Support of Corporate Mandated Environmental Stewardship and Sustainability goals
A local manufacturer of the titanium screws used in spine fusion required deburring in their manufacturing operation. In the interest of supporting Corporate Mandated Sustainability goals and the many benefits of recycling, they sought a Zero Liquid Discharge(ZLD) solution. Due to the moderate volume of solids generated from this specific operation, AQUASGROUP’s GFS VRS-WW System was installed, which incorporates a unique non-fouling ultrafiltration technology. The recycled water and compound produced by the GFS VRS-WW System is glass-clear and is used repeatedly for months on end.
On higher solids load applications, we use our GFS-VRS-C-WW, which includes an automatic centrifuge as the primary method of gross solids removal. And on light loads, we apply our simple gravity settlers, packaged in convenient, disposal containers, to simplify your ZLD objectives.
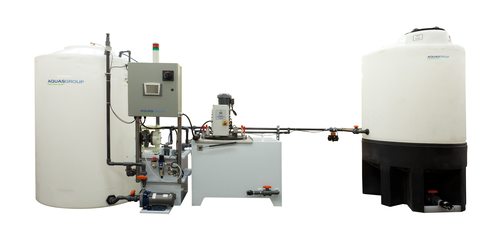
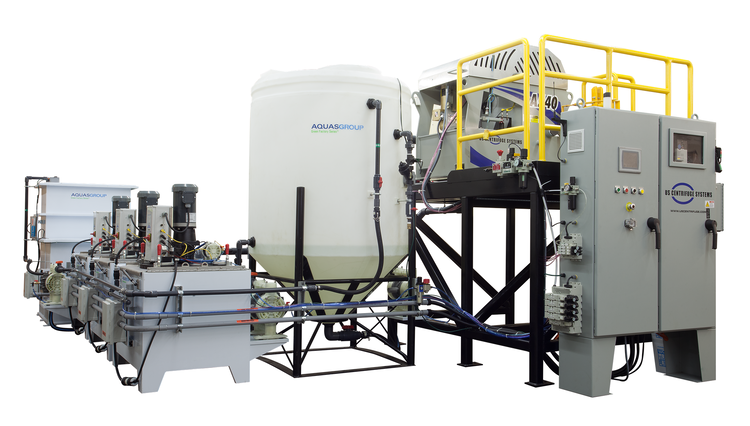
This GFS-VRS System was installed in 2014 and has been a reliable source of recycled compound and water, free of solids, ever since. AQUASGROUP has installed many additional GFS-VRS Systems at facilities throughout New England and the US.
AQUASGROUP is eager to work with you to evaluate opportunities for waste minimization and process water recycling in your manufacturing operation. Please contact us to discuss your manufacturing requirements as it relates directly to recycling water, quality and the future of manufacturing.
Engineering
Nicholas Paolo, Jr.
President / Engineering
Mailing Address:
AQUASGROUP
830 Waterman Avenue
East Providence, RI 02914-1728